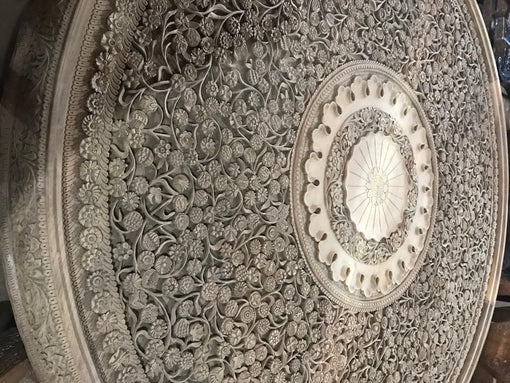
- Article published at:
- Article author: Hamiast Global
- Article comments count: 1
Drawer menu
Kashmiri Wicker Willow Craft
Wicker is the term used for products made by weaving and twisting thin slices of woods together. When such products are manufactured using willow wood, the craft is known as wicker willow. In Jammu and Kashmir, these intricate handmade wicker willow products are commonly referred to as Veer Kani or Keani Keam.
Artisans of Jammu and Kashmir state are known worldwide for making baskets, more commonly known as Kangri, using willow woods. Kashmiri Kangri was originally used by natives, especially farmers and tribal people, for carrying clay pots containing smouldering coal. They hold hot clay pots in these baskets beneath their long flowing cloths or pherans. It protects them from cold and keeps their body warm during the winter season.
Now the art has gained widespread popularity and is commercialised for making various other home decor items like chairs, tables, etc.
History of Wicker Willow Art
The origin of wicker manufacturing dates back to Sumerian Civilization in 400 BC. They used wicker woods for various purposes such as transport, housing, home decor, utensils, etc. However, evidence of wicker willow as an art form has been found in ancient Romans and Egyptians’ history.
The oldest wicker furnitures that are present today are of Egyptian origin. Some examples include wicker chairs and hassocks, chests manufactured from rush and reed, and papyrus wig boxes.
In Jammu and Kashmiri, this art was introduced in the 19th century. Natives believe that Maharaja Hari Singh brought 12 kgs of seeds and skilled craftsmen from Europe for making beautiful wicker willows.
Before this, Kashmiris produced wicker willow baskets to help farmers. They needed a basket for storing and transporting goods. The state had rich forest and vegetation. So, tribal communities used local grasses, i.e., willows, for making mats and baskets.
These tribal communities used a method known as Kangri for manufacturing such baskets. This is why the baskets made from willow wood in Kashmir are known as Kashmiri Kangris. Kalhana Rajatarangini is the first book known in history that talks about this process. It is one of the many popular books that traces Kashmiri history.
It mentions that Suyya, a renowned engineer, regulated the path of the Jhelum river using Kangri technique to save the villages from flooding. This happened between A.D. 855 and 883 under the rule of Raja Avanti Verman. Suyya made circular dykes around villages which protected them from the flood.
Mr Andrews, a Britisher, established a technical institute in Srinagar around 1914-16 to introduce the English technique of wicker weaving in the area surrounding Bage-Dilawar Khan. The present-day willow weaving in Kashmir has evolved from the teachings of that institute.
Manufacturing Process of Kashmiri Wicker Willow
Although the willow weaving art is commercialized, artisans still use traditional techniques to make wicker products. Some modifications have been made to increase the sales value of products. Step by step process of handmade willow weaving is described below:
Current Trends of Handmade Wicker Willow
Now the usage of willow woods is not just limited to manufacturing Kashmiri Kangris. Craftsmen make other products using this plant, such as picnic baskets, tiffin boxes, lampshades, chairs, tables, trays, curtain rings, and cycle baskets.
Artisans majorly follow two weaving processes for producing aesthetic wicker willow products:
Traditionally, the artisans dyed wood in various shades, especially blue, red, and green, to give baskets and other products a colorful appearance. They make geometric patterns via careful multi-directional weaving. Embellishments such as mirrors, foils, and metal pieces are added to beautify Kangris.
However, nowadays, plain willow wickers having softwood colors are also very much in demand because of the aesthetic and natural feel. Thus, you may find chairs, tables, baskets, lampshades, etc. of willow wood color also in the market.
Both of the varieties mentioned above are available for purchase on the Hamiast website.
Conclusion
The best part about willow wicker artform is that it is not mechanised yet. Artisans still use the handcraft for delicate interweaving of willow stems for making aesthetic products. Also, wickers made from willows not only look beautiful but also have a real utility. These products are sturdy enough to withstand the weight of other objects.
Hamiast offers a range of home decors made by skilled Kashmiri craftsmen of willow wicker art. You just have to find a perfect one to enhance the charm of your beautiful home.